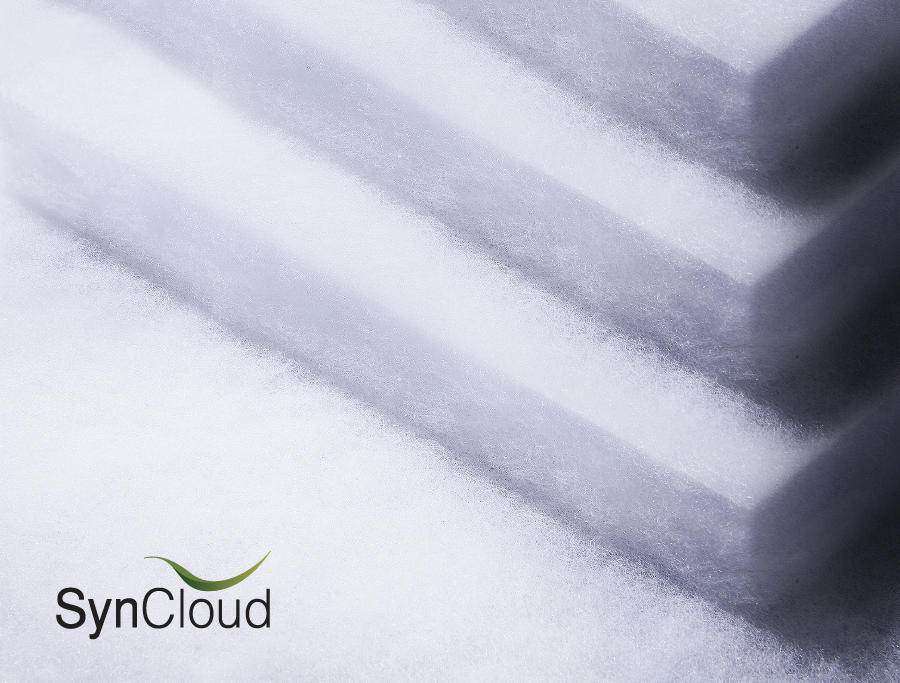
Synthetic Insulation Production Process: Part 2. Processing
2020-09-02
The “Synthetic Insulation Production Process” series is intended to help you better understand the material. This article focuses on the second step, processing.
Link: Synthetic Insulation Production Process: Part 1. Raw Materials
Synthetic insulation production processes vary by its form, as shown in the figure below. The following texts are an overview of form-specific production processes.
<Synthetic insulation processing by form>
Sheet Type
1. Fiber preparation
There are numerous types of staple fibers, the raw source of insulation, in terms of ingredients, length, crimp, and processing methods. The product development stages involve tens or hundreds of tests to materialize the characteristics of insulation and make decisions on the types of ingredients, mixing ratios, and processing methods. The resulting production manual determines how staple fibers are prepared.
The staple fibers are delivered as pressed bales. Put in the machine, they move along the conveyor system and are split into small lumps. Later on, different types of staple fibers are mixed by the wind in the blending box.
<Inlet (left), blending box (right)>
2 .Web forming
The mixed staple fibers move along the conveyor system. Cylinders with needles densely placed on their outer surface rotate and comb the staple fiber bunches on the conveyer to unroll. This process is called “carding.” The thinly-spread staple fibers fall between two cylinders that move at a steady speed in a zig-zag shape to form layers. This process is called “cross lapping”. The thickness of insulation depends on the machine operation speed and the number of layers. This is an important process to ensure staple fibers in the accurate weight are evenly distributed.
<Carding (left), cross lapping (right)>
3. Web bonding
To make the staple fibers bind well, a liquid-form resin is sprayed evenly on them, followed by heat-drying. This process is done on both sides of the sheets to improve their durability. Care should be used, as they may stick to each other if not completely dry. SynCloud uses environmentally-friendly OEKO-TEX-certified synthetic resins only.
4 .Web finishing
For finishing, heat is applied to the surface of the sheets to make the surface even and prevent the staple fibers from escaping. The higher temperature, the stronger fixing power on the surface but in return for less volume and rough surface textures.
Recently fabrics used for clothes are increasingly thin, and oftentimes padding bags are omitted for a better feel. In this case, the exudation of insulation can be prevented by applying higher heat in the finishing process to fix them tighter.
The finished insulation is rolled and compressed for storage. A typical roll is 60-inch wide and the unit of the length is yard. It usually weighs seven to ten kilograms.
<Web finishing>
Cloud Type
<Fiber opening machine>
The preparation of the staple fibers is the same as sheet-type insulation. The staple fibers are put in the fiber opening machine for the carding process, where cylinders rotate to open them. This process may look simple but requires meticulous care and quality control. Wad of fibers remaining would mean insufficient volume and lumping of insultation in finished garments.
Ball Type
Cloud-type insulation is put in the fiber ball machine. During this tumbling process, round ball-type insulation is made. The longer tumbling, the smaller and harder balls made. The materials should be processed for the right time to have the right shape for their intended purposes.
*Image source: AUTEFA
By Park Kyung-jun, SynCloud Part