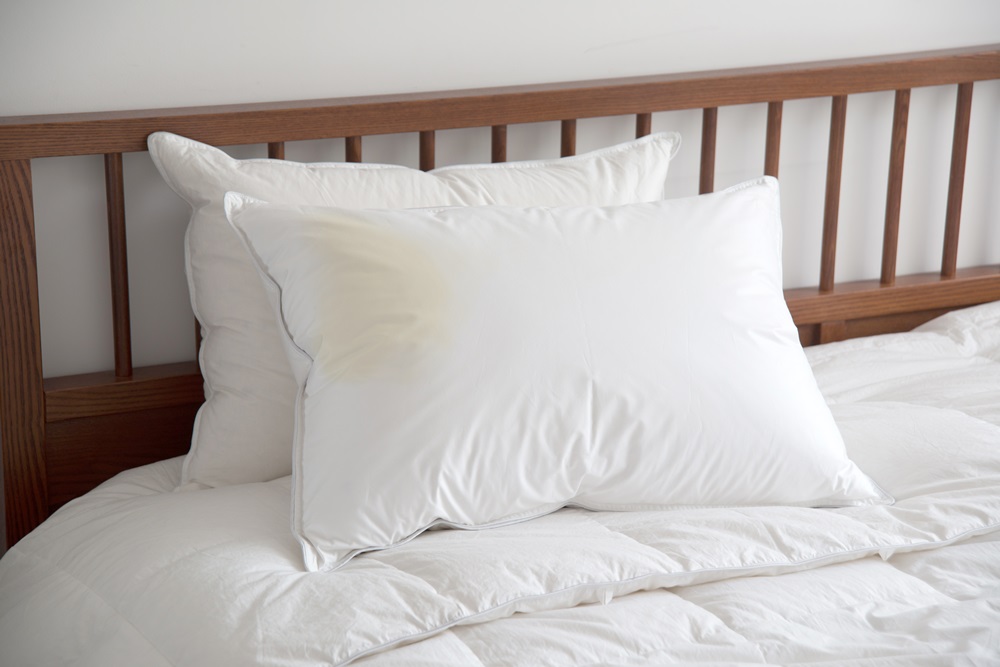
Things to note about down product discoloration
2021-04-13
Textile products may suffer discoloration caused by various factors, for example sunlight, sweat, antioxidants, or stickers. Here are some tips to avoid discoloration.
What is discoloration?
Discoloration of textile products occurs when they are exposed to chemical reactions or sunlight, leading to changes in color. Oftentimes white or pale-colored products are devoured by discoloration, but products in darker colors may experience discoloration, shown as yellow, brown, blue, red, or orange stains. Commonly affected areas include padding cloth, collars, folded edges, sewing threads, parts in contact with cloth hangers or packing materials, or the whole product itself.
<Discoloration after washing>
When the fabric’s air permeability is low
Air permeability means the level of air penetrating through the air holes in the fabric. Down materials hold air to exert thermal effects, so fabrics filled with down should have air permeability to a degree.
When fabrics that are designed not to allow air or moisture to pass through are filled with down, they may experience discoloration after washing.
During the post-washing drying process, the poor air permeability of the fabrics means a longer time to dry, and washing residues remain undried in certain areas of the product, leading to discoloration.
<Discoloration on the outer fabric after washing>
<Water pressure resistance and air permeability tests.
The test results for #1 are for the outer fabric of the discolored product. >
To avoid discoloration, it is advisable to use fabrics with good air permeability. When applying coats to fabrics or using fabrics with wind-blocking and water-repellent properties for outdoor activities, doing washing tests with finished products is a must, as typical cushion-shaped mockups are simple in structure, hence difference in drying time from finished products.
A product may not suffer discoloration when tumble dried but may be discolored when line dried. In this sense, recommending machine drying right after washing in the care label helps the customer better care for the product.
<Post-washing drying test. No stains when machine washed and tumble dried.>
When inadequate packing materials are used
Discoloration may be caused by packing materials used for clothes.
PE, PP films: They are used as primary packing materials for textile products, and many additives are added to them during the production process, for example antistatic agents and ultraviolet absorbents. Among them, butylated hydroxy toluene (BHT) used as an antioxidant may cause discoloration. Having strong sublimation properties, BHT is attached to the surface of the textile and reacts to nitrogen dioxide in the atmosphere, resulting in discoloration.
<Discoloration caused by antioxidants>
Paper: Boxes or fillings made from paper has a large amount of lignin originated from pulp. As a phenolic polymer, lignin contained in paper turns yellowish-brown triggered by temperature, humidity, or light, as seen in old, yellowed newspaper.
<Phenolic yellowing fastness test for fabrics from store-released products discolored before washing.
Test results ≤ 3 mean potential phenolic discoloration.>
<Pre-test fabric (left), post-test fabric (right)>
There are so many factors that may cause textile products to be discolored. To avoid discoloration, thorough considerations should be given to product planning, including materials selection, product design, packing, shipping, and washing instructions.
By Lee Sukyung, Brand Part