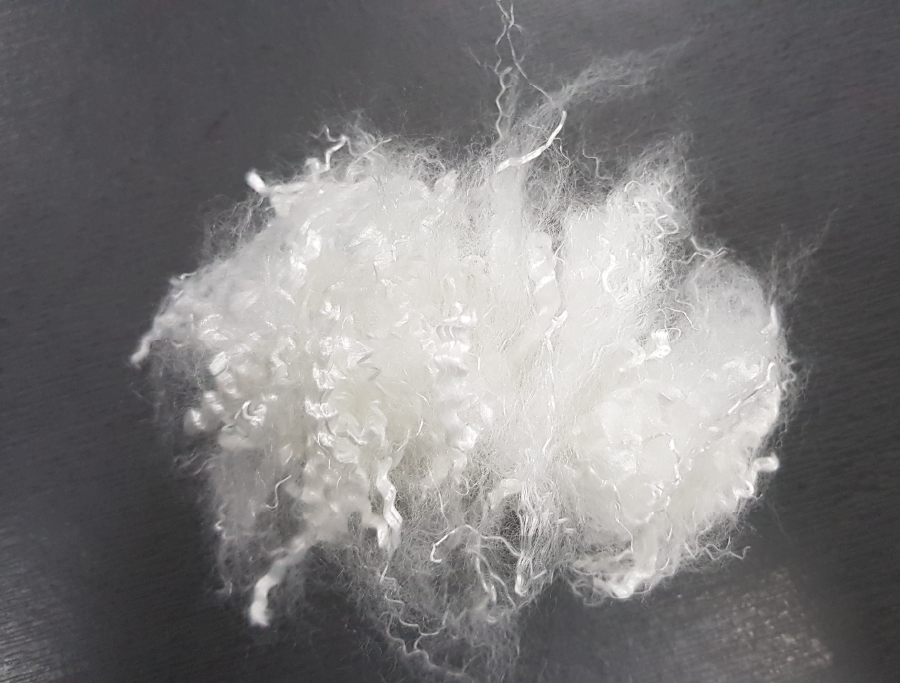
합성 충전재 생산 공정 1. 원료 편
2020-05-19
의류 기획 단계에서는 소재에 대한 이해가 필수적이다. 소재의 특성을 알아야 기획 의도에 적합한 소재를 사용할 수 있으며, 그 장점을 잘 활용할 수 있기 때문이다.
이러한 이해를 돕기 위해 이번 호부터 ‘합성 충전재 생산 공정’을 3회에 걸쳐 소개하려고 한다. 1) 원료 생산 단계, 2) 가공 단계 및 최근 높은 수요가 있는 3) 리사이클 원료 생산 단계 순서로 진행된다.
섬유는 길이에 따라 장섬유(filament)와 단섬유(staple fiber)로 구분된다. 길이가 긴 장섬유는 원단에 사용되며, 합성 충전재는 길이가 짧은 단섬유를 가공하여 만드는데, 이 단섬유를 만드는 과정을 살펴보자.
*폴리에스터에 많이 사용되는 용융방사(Melt Spinning) 기준으로 설명한다.
<단섬유의 생산 공정>
이미지 출처: 휴비스
1. 중합(Polymerization)
석유에서 얻어진 액체 상태의 에틸렌글리콜(Ethylene Glycol, EG)과 분말 상태의 고순도 테레프탈산(Purified Terephthalic Acid, PTA)을 혼합하여 열과 압력을 가한다. 이 중합 반응을 통해 겔(Gel) 형태의 폴리머(Polymer)가 된다. 이것을 바로 방사하기도 하고 칩(Chip) 형태의 레진(Resin)으로 만들기도 한다.
2. 방사(Spinning)
열로 레진을 녹이고 압력을 가해 미세한 노즐 구멍을 통해 밀어내어 실 형태의 폴리에스터 원면을 만든다. 노즐의 크기에 따라 섬유의 굵기가 결정되는데, 굵기가 가늘어질수록 더 높은 기술력이 필요하다.
<방사 장면(좌), 방사용 노즐(우)>
3. 연신(Drawing)
폴리에스터 원면을 롤러로 당겨서 길게 늘인다. 이후 강하게 당겼다 푸는 방식으로 텍스쳐링(Texturing)을 하여 제품에 벌키감을 높이는 꼬임(Crimp)을 주게 된다. 연신은 제품의 품질을 결정하는 중요한 공정이다.
<연신 공정>
<텍스쳐링 된 폴리에스터 원면>
4. 절단(Cutting)
수분, 약품 등이 남아있는 원면을 드라이어로 건조한 후 일정한 길이로 절단하는데 이것이 단섬유이다. 일반적으로 22~102mm 사이의 길이로 절단하는데, 짧은 길이의 섬유는 추후 솜 형태의 충전재로, 긴 길이는 시트 형태의 충전재로 가공된다.
섬유의 길이가 너무 짧은 경우에는 꼬임이 충분히 잡히지 않아 벌키성과 회복성이 낮고, 또 너무 긴 경우에는 이를 완제품에 충전했을 때 섬유끼리 뭉칠 수 있다. 그래서 원료 생산 단계에서부터 제작할 충전재의 형태와 특성을 고려하여 단섬유의 길이를 결정해야 하며, 이 단계에서 충전재 생산 업체의 노하우가 제품의 품질에 큰 영향을 미치게 된다.
<단섬유의 모습>
5. 포장(Packing)
일정한 무게로 압축하여 포장한다. 제품의 벌키성에 따라 다르지만 보통 250~320kg이 1개의 묶음(bale)이 된다.
<포장이 끝난 모습>
충전재의 특성은 원료 단계에서 많은 부분이 결정되므로 원하는 특성을 발휘할 수 있는 충전재를 만들기 위해서는 원료의 세부적인 발주와 품질 관리가 필요하다. 신클라우드는 20년 이상의 노하우를 가지고 원료 단계에서부터 충전재에 적합한 원료로 가공될 수 있도록 양질의 원료 업체와 긴밀하게 협력하고 있다.
By 신클라우드 파트, 박경준